At C.O.B.O., digitalization has taken the continuous improvement process to the next level: paper-based workflows have been replaced by Visual Shop Floor – with real-time KPIs, automated reports, and interactive shop floor boards. Asaichi meetings are now more structured, faster, and more effective. This way, Kaizen at C.O.B.O. is not just practiced – it's actively driven forward.
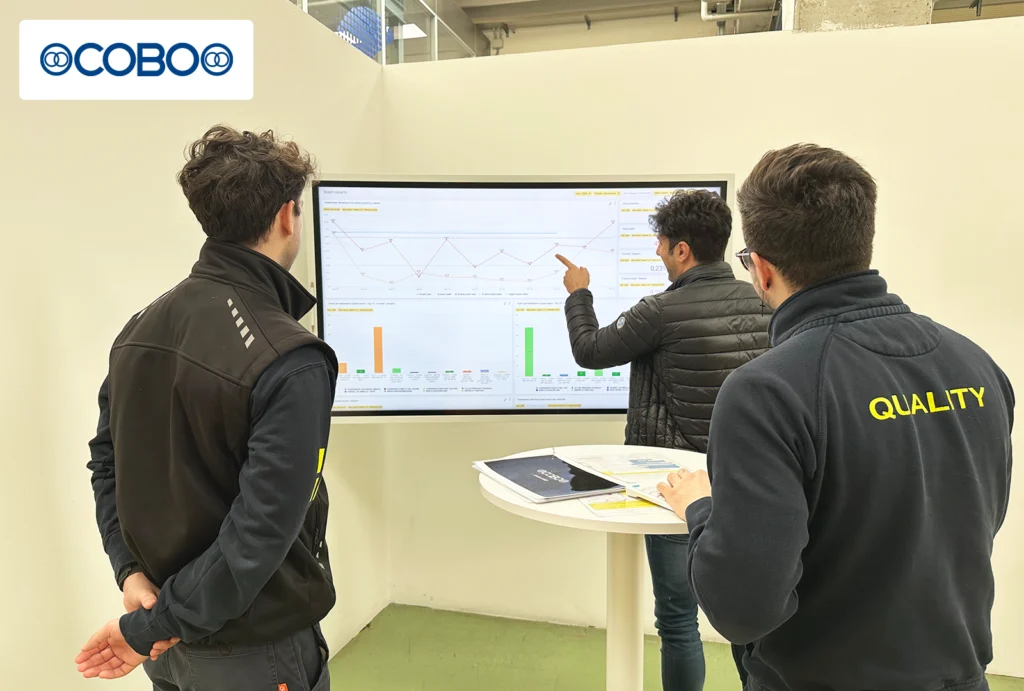
C.O.B.O., Visual Shop Floor in action – Info Board
C.O.B.O., present in the industrial vehicle markets and an increasingly valued partner in the automotive sector, is a leader in the design and production of complete equipment and connectivity services for an integrated machine system. The company supplies major commercial vehicle manufacturers in over 75 countries worldwide. Founded in 1952 and headquartered in Leno (Brescia), the company employs over 1,500 people and operates 11 production facilities.
C.O.B.O., headquarter, Leno, Brescia
Challenge
- Outdated KPIs in paper-based documents
- Delayed communication between departments
- Limited transparency in tracking corrective actions
- High time expenditure in managing improvement processes
Solution
- Automated KPI calculation with real-time notifications and reporting
- Structured Asaichi meetings with up-to-date KPIs
- Interactive and specific shop floor boards in each department
- Systematic and structured task management
Result
- Time savings through automation of recurring manual tasks
- Optimization of planning and implementation of corrective actions
- Increased efficiency through digitization of paper-based shop floor boards
- Enhanced sustainability by reducing paper consumption
- Establishment and broader application of Kaizen principles
Paper-based processes – a stumbling block for Kaizen
Analyzing disruptions and deviations, collecting KPIs, assigning and tracking improvement actions – all on paper? For C.O.B.O., a global leader in integrated systems for the off-highway vehicle market, this is no longer an option.
Before adopting Visual Shop Floor, information at C.O.B.O. was largely managed through paper-based processes. It was difficult to ensure consistent, reliable data across departments. Data had to be manually gathered from various systems, transferred on paper, and quickly became outdated or incomplete – undermining decision-making and improvement efforts.
Managing actions was equally inefficient. “Actions and responsibilities were written by hand on a board – but following through on them depended entirely on individuals,” explains Matteo Boccanfuso, World Class Manufacturing Coordinator – Focused Improvement and key user during the implementation of Visual Shop Floor.
The need for a digital solution was evident. The goal: replace paper-based boards as the main source of information and transform the daily Asaichi meetings – where cross-functional teams align – into a more efficient, transparent, and collaborative tool to drive continuous improvement (Kaizen) across the organization.
Digitalization and automation of production processes
Efficient management of production processes requires more than just data collection — it demands thorough processing, meaningful consolidation into key performance indicators (KPIs), and clear, intuitive visualization to ensure maximum transparency, all delivered continuously and automatically. This is exactly where Visual Shop Floor makes a difference at C.O.B.O. What was once handled via paper lists and handwritten notes has now been replaced by an intelligent digital solution that seamlessly integrates all workflows.
Thanks to the flexibility of Visual Shop Floor, C.O.B.O. can independently address a growing range of use cases. “Today, we leverage Visual Shop Floor to systematically analyze the root causes of machine breakdowns and other critical events (EWO – Emergency Work Order), efficiently manage maintenance and service orders, and comprehensively document and evaluate safety incidents (S-EWO – Safety Emergency Work Order) as well as improvement proposals,” explains Matteo Boccanfuso. An Emergency Work Order (EWO) is an urgent work instruction created, prioritized, and assigned to the responsible team for immediate resolution of disruptions.
A further key feature is the automated generation of notifications and reports on critical topics such as quality issues, test results, scrap rates by area and month, and delays in maintenance activities. What was previously compiled manually through time-consuming efforts now runs entirely automatically. Responsible personnel receive a complete overview of all ongoing activities — directly linked to their respective projects in Visual Shop Floor. “This not only saves us valuable time by automating repetitive tasks but also significantly reduces paper consumption. With Visual Shop Floor, we have taken a decisive step forward in the digital transformation of our Shop Floor Management,” concludes Matteo Boccanfuso.
Visual Shop Floor has allowed us to completely replace our paper-based boards. With always up-to-date information, we can fully focus on continuous improvement (Kaizen)."
Matteo Boccanfuso,
WCM Coordinator – Focused Improvement, C.O.B.O.
Efficient Asaichi meetings – the key to continuous improvement
Since its introduction, Visual Shop Floor has become a key pillar of continuous improvement (Kaizen) at C.O.B.O. “Having real-time information is essential for running our daily Asaichi meetings in a structured and efficient way. It allows us to focus our efforts and drive sustainable process optimization,” explains Matteo Boccanfuso.
With Visual Shop Floor, the daily Asaichi meetings – where cross-functional teams come together – have become noticeably more effective. Information is presented in a clear and structured format, and actions can be initiated immediately thanks to the integrated task management tools. Tasks are assigned and tracked in real time during the meetings, enabling better workload management, preventing overloads, and reducing inefficiencies. At the same time, the transparent visualization of all actions ensures that nothing falls through the cracks – an essential advantage for faster decision-making and the sustainable implementation of improvements. This is how Matteo Boccanfuso summarizes the key benefits that Visual Shop Floor has brought to C.O.B.O.
Next steps – from implementation to a cross-site solution
During implementation, C.O.B.O. set a clear objective: to capture the specific needs of each department and translate them into tailored solutions. Through a detailed analysis of internal processes, all relevant factors were carefully considered – ensuring a seamless rollout and enabling Visual Shop Floor to be rapidly and efficiently adopted across the entire organization.
“Our future plans for Visual Shop Floor include expanding its use to additional plants and external sites,” says Matteo Boccanfuso. “This won’t just strengthen inter-site collaboration – it will also help embed Kaizen thinking more deeply throughout the company.” In the long run, C.O.B.O. aims to establish Visual Shop Floor as a core pillar of its digital transformation strategy – driving greater efficiency and continuous improvement on a company-wide scale.
Why C.O.B.O. chose Visual Shop Floor:
Summary by Matteo Boccanfuso,
WCM Coordinator – Focused Improvement, C.O.B.O.
Comprehensive identification of requirements
"Through an in-depth needs assessment and thorough process analysis, the specific demands of each department were clearly defined. Visual Shop Floor enabled these requirements to be transformed into precise, customized solutions that effectively support the company’s goals."
High flexibility and rapid deployment
"Thanks to Visual Shop Floor’s no-code/low-code configurability, the system was quickly implemented using existing in-house resources. This minimized the effort required for deployment and allowed for an agile, practical approach."
Simple adoption and strong user acceptance
"With its user-friendly interface and intuitive design, employees were able to adopt Visual Shop Floor quickly and effortlessly. This led to high user acceptance and a smooth implementation across the entire organization."
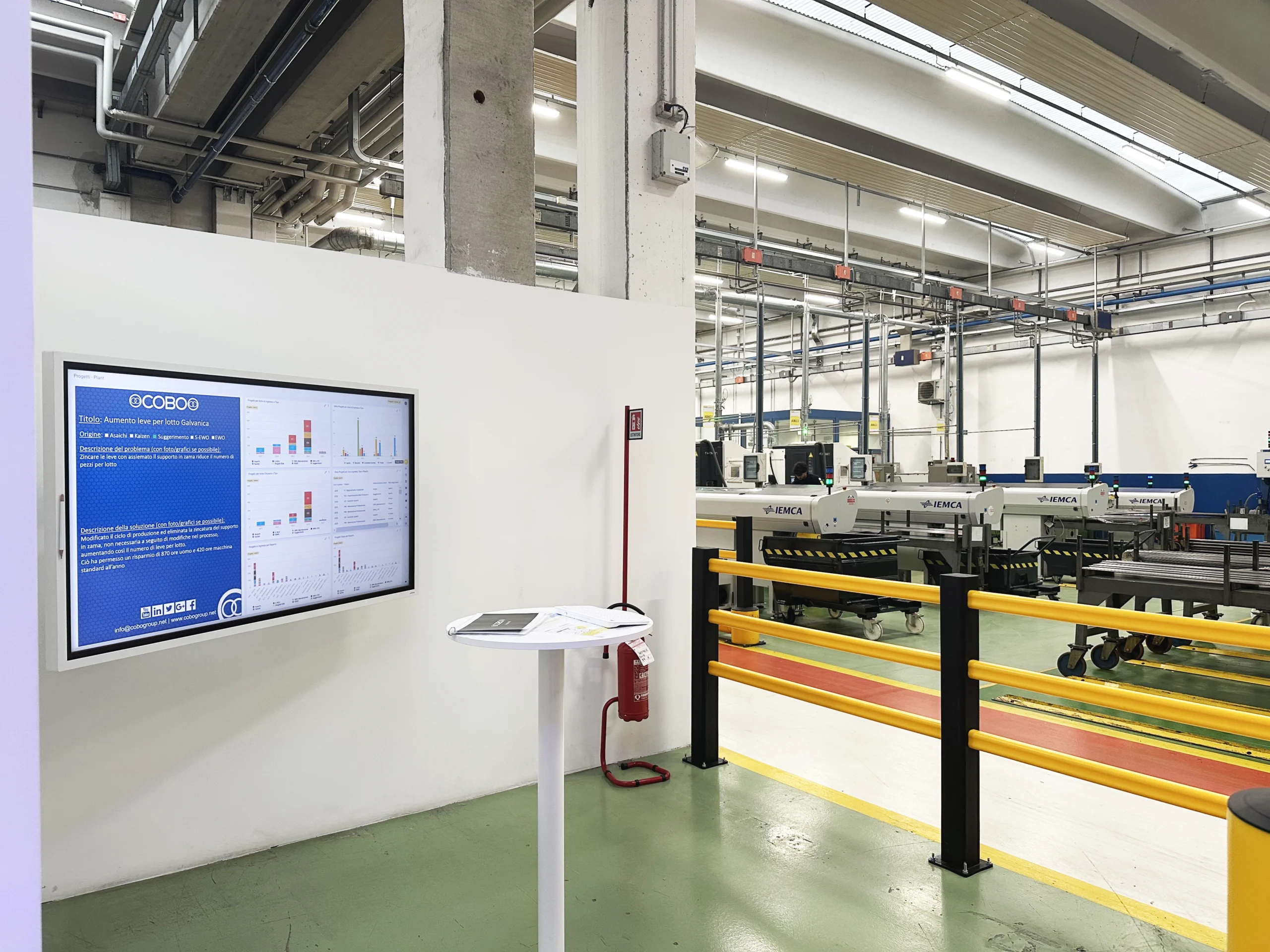
Visual Shop Floor – Info Board in production at C.O.B.O.