The internationally active Intercable Group has been relying on digital Shop Floor Management with Solunio's software Visual Shop Floor since 2016. It obtains information from eight IT systems, prepares important key figures clearly and makes them available to managers and employees in real time based on their roles. With considerable growth, the company benefits from stable processes, higher Overall Equipment Effectiveness (OEE) and significantly lower error costs.
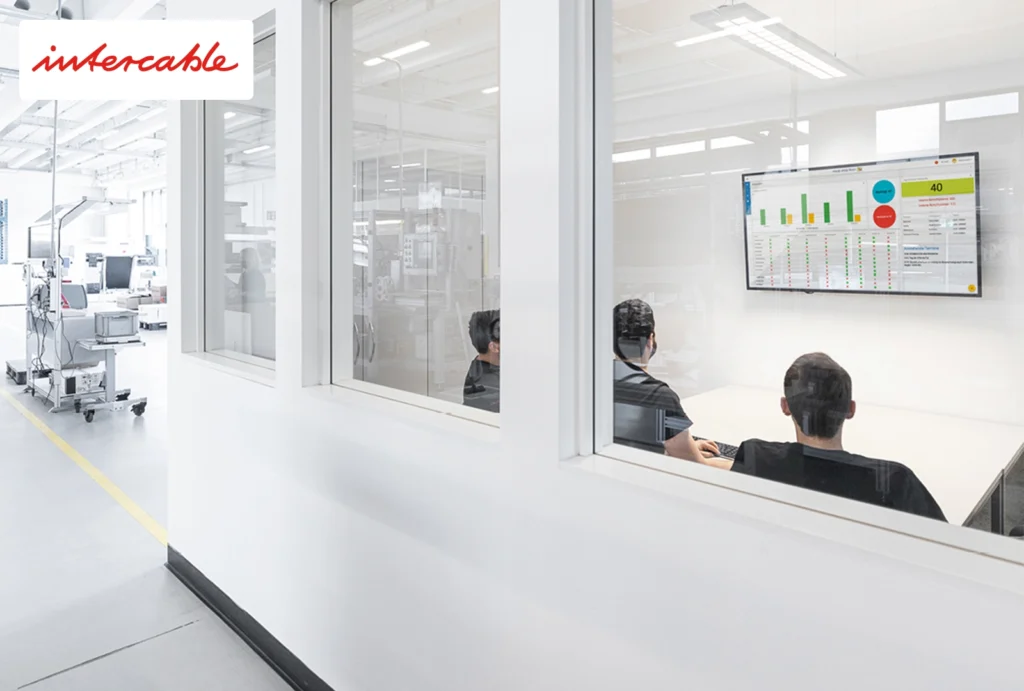
Intercable, Visual Shop Floor – Shop Floor Meeting
Founded in 1972 in Brunico (South Tyrol), Intercable Ltd. today operates as a global player with two mainstays: Intercable Tools develops and manufactures tools for processing low and medium voltage cables as well as connecting materials for the electrical, wind and railroad sectors. Intercable Automotive has been producing plastic parts and cable protection systems for the automotive industry since the early 1990s.
With customer-specific tooling, innovative plastic injection molded parts and a zero-defect quality target, the Tier 1 supplier of high-current components for electromobility at the Bruneck site grew from 120 employees in 2008 to 800 today, with a further 700 employees spread across plants in Slovakia and China.
With customer-specific tooling, innovative plastic injection molded parts and a zero-defect quality target, the Tier 1 supplier of high-current components for electromobility at the Bruneck site grew from 120 employees in 2008 to 800 today, with a further 700 employees spread across plants in Slovakia and China.
Intercable, headquarter Bruneck
Challenge
- Complex production processes
- Lack of centralized data accessibility
- Fragmented data landscape
- Unclear priorities and planning errors
Solution
- Involvement of all management levels
- Manageable pilot project
- System expansion throughout the company
Result
- Rapid ROI
- Increase OEE
- Lower scrap costs
- Immediate response to deviations from key figures
Growing challenges
Interlinked, multi-stage production processes such as die casting, punching and welding, finishing, assembly, packaging and shipping are difficult to keep track of. Extensive data on machines, employees, quality processes, output and rejects are generated and processed in systems ranging from PDA to CAQ and ERP. “But these are all isolated solutions,” says Patrick Abfalterer, Automotive Assembly Department Manager at Intercable. “Those responsible were missing important data and key figures, which they had to laboriously gather from various systems.”
When faced with problems from strong company growth and increasing quality requirements, they did not always focus on the right processes, machines or production areas. “The priorities were not clearly evident,” says Patrick Abfalterer. “The consequences were unrest in production and planning errors, incorrect distribution of competencies and capacities.”
Germ cell in the automotive assembly hall
In 2016, the company decided on an Industry 4.0 project with the software manufacturer Solunio, also based in Bruneck, and its Visual Shop Floor software. The digital tool for the lean discipline of Shop Floor Management creates transparency – for employees and managers. Data is taken from the existing systems, machine controls and sensors and processed according to the customer's information needs. The information obtained is continuously displayed on dashboards and is used to prepare for daily Shop Floor Meetings or for process automation.
“In preparation, we defined the desired key figures on Overall Equipment Effectiveness (OEE), quality trends and productivity as well as the corresponding data sources including eight different IT systems,” Patrick Abfalterer reports. “Likewise, we had to determine the exact information needed along our management structure.” To keep the project manageable, the first step was to start with the automotive assembly hall. There, around 70 employees work on 43 systems, which mainly comprise special machines, in various manufacturing and assembly processes.
From pilot project to widespread implementation
After the successful pilot project, the use of Visual Shop Floor has now been extended to all halls and production areas at the Bruneck site. As a result, the top management, including the two sons of the company founder, Klaus and Kurt Mutschlechner, can now access all key figures, such as the current OEE, on a daily basis. The introduction in small, manageable steps and the transfer of the successful projects to other halls and areas has proven successful for Patrick Abfalterer: “You save on large-scale planning and concepts and duplicate the successful components. Thanks to the training of our employees on Visual Shop Floor, we can implement these changes and additional projects even without Solunio.”
I can see at a glance the current order status at every workplace!”
Patrick Abfalterer,
Head of Automotive Assembly, Intercable
Real-time transparency
After about a year, each employee had a terminal at his or her workstation with all the information for the respective job. Current key figures on quality, output, break times are just as much a part of this as information and regulations on the often customer- specific work processes. “In addition, I can send messages and notifications to any workstation at any time,” Patrick Abfalterer is pleased to say. “Moreover, each management level receives its own view of all the data relevant to its area.”
The digital hall mirror with all workstations provides a constant overview of the situation in production. “I can see at a glance the current order status at each workstation, which employee is at which system, and where malfunctions or bottlenecks are occurring,” says Patrick Abfalterer. “This makes it possible to react faster and make better decisions.” From there, he can call up detailed views of areas, machine groups or workstations. From shift planning to setup processes and sampling to the digital quality matrix, all areas were gradually integrated.
Rapid Return on Investment (ROI)
Over the past two years, Intercable has seen numerous positive effects in various areas. “Our production processes are running smoother and more stable,” Patrick Abfalterer summarizes. “We have been able to increase OEE significantly. Most importantly, we’ve been able to amortize our entire effort through lower scrap costs alone.” Shutdowns and production interruptions have become less frequent, and it has been possible to react more quickly than before when plant problems arise. “As soon as individual key figures show deviations, we take action.”
Visual Shop Floor is becoming the central source of information, so that other production-related systems are no longer rolled out and used to the same extent as before. So it’s no surprise that in the medium term, all of the company’s 17 subsidiaries and sites are expected to benefit from Visual Shop Floor.
Layered Process Audits – Implementing process standards
In close collaboration between Intercable and Solunio, the project to implement Layered Process Audits in Visual Shop Floor was successfully completed. The goal was to ensure adherence to and implementation of process standards at all management levels within the plant. This integration into Visual Shop Floor enables systematic and continuous monitoring of processes, with all management levels actively involved in the auditing process.
"How to introduce Visual Shop Floor correctly",
Tipps from Patrick Abfalterer,
Head of Automotive Assembly, Intercable
01.
Clear definition of key figures02.
Designate responsible persons from IT and someone for each department03.
Inform all levels about the purpose of the system04.
Select the systems that will be integrated05.
Select data and information for each management level06.
Aquire Andon Boards or terminals to inform production07.
Establish clear management structure, such as department management, shift management, setters, and workers, and develop precise role profiles08.
Select only the necessary information for maximum transparency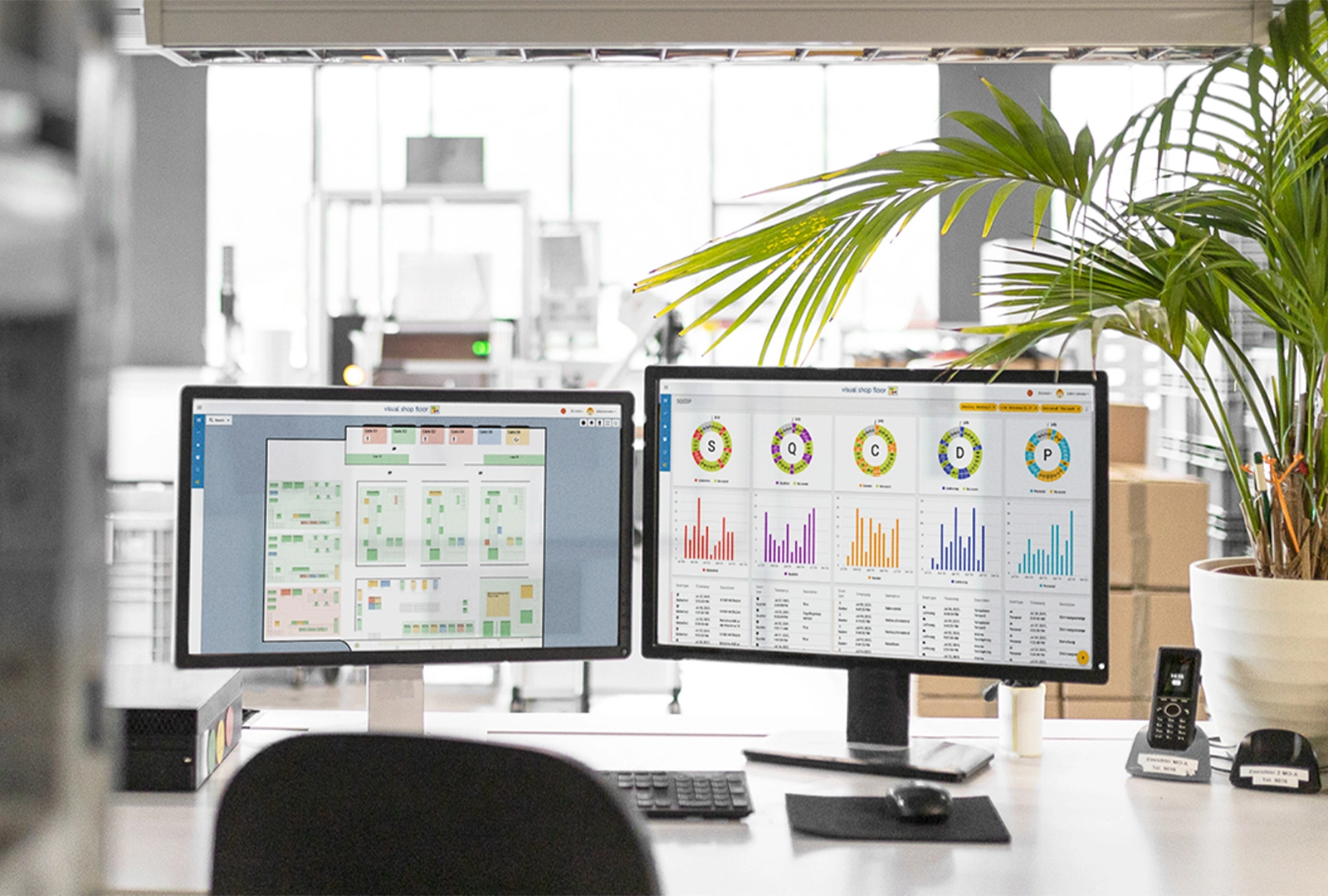
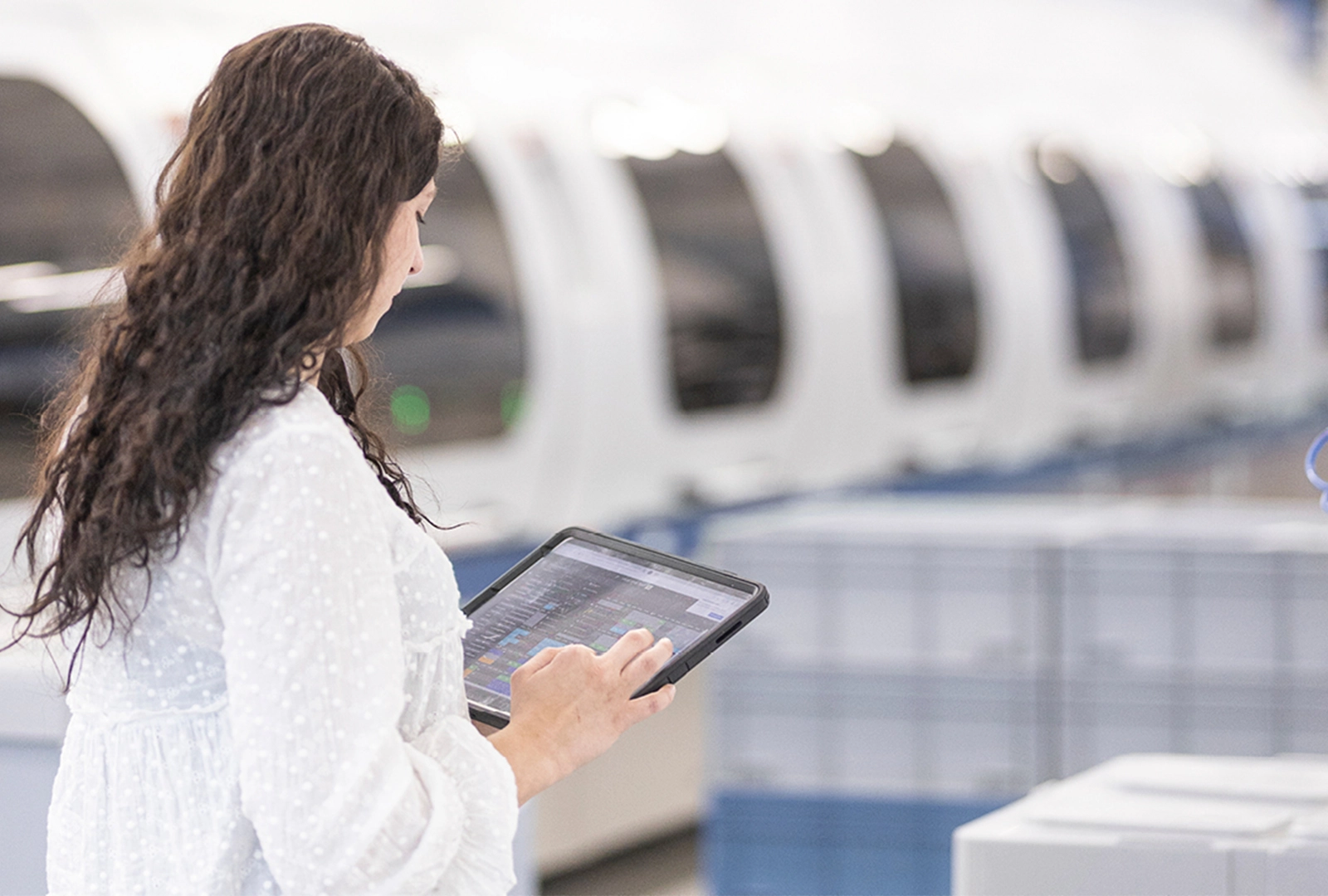
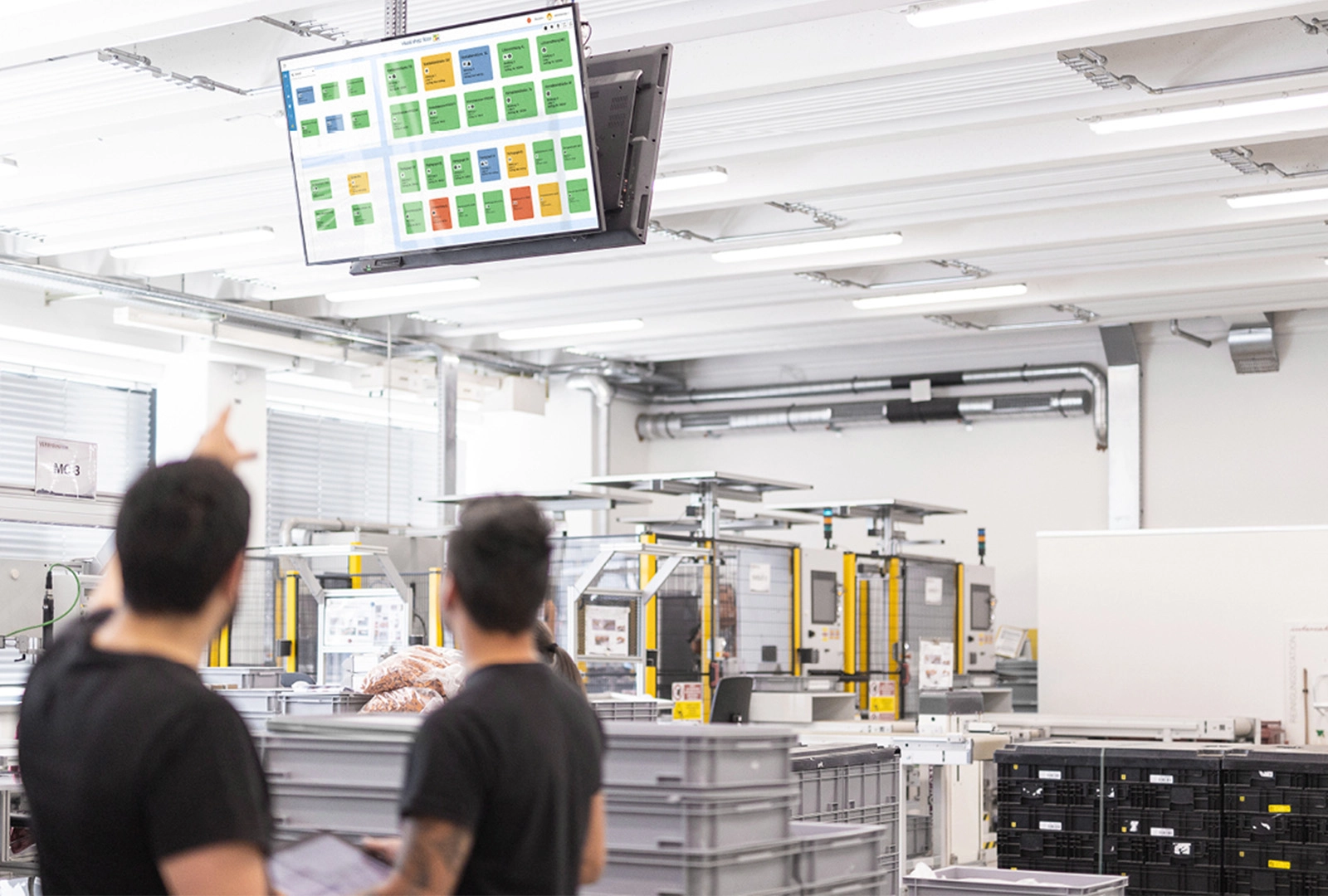