At TDK Electronics, the software platform Visual Shop Floor is primarily used to visualize all production-relevant information in real time, enabling the company to take timely and targeted countermeasures. This allows the company to efficiently integrate new requirements and challenges into Visual Shop Floor and successfully overcome them.
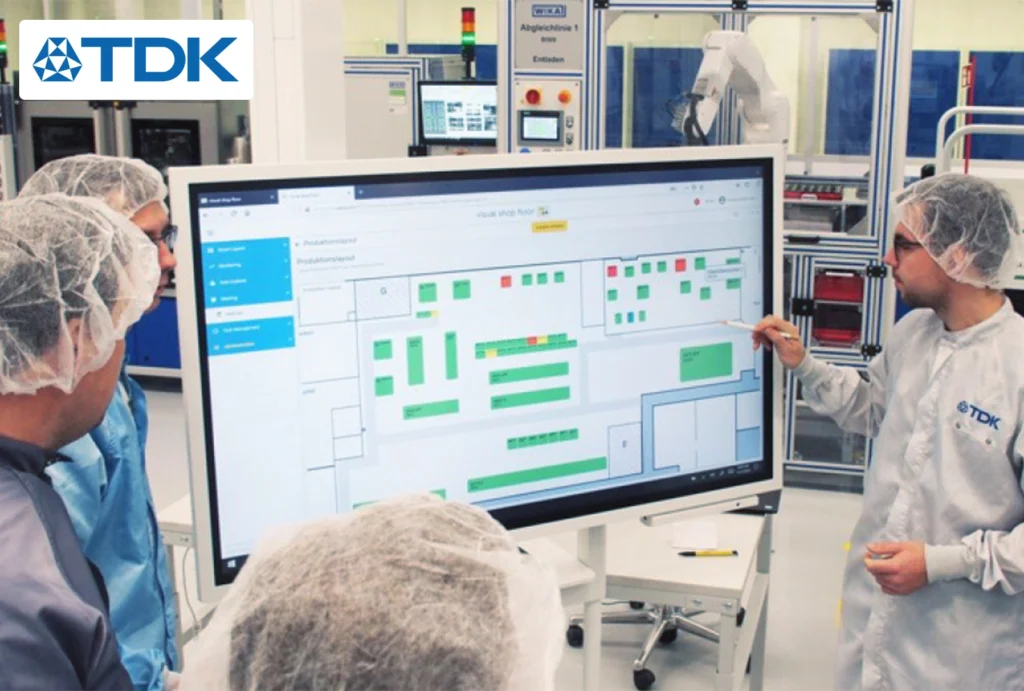
TDK Electronics, Visual Shop Floor – Digital hall mirror
TDK Electronics develops, manufactures and markets electronic components and systems focusing on fast-growing leading-edge technology markets, which include automotive electronics, industrial electronics and consumer electronics as well as information and communications technology. The company is positioned globally and close to its customers, employs more than 22,000 people at around 20 development and manufacturing sites.
TDK Electronics, Plant Berlin, Germany
Challenge
- Slow adaptation to new requirements
- Low transparency and flexibility in manufacturing
Solution
- Information accessible on PC, tablet, and smartboard
- Meeting module for daily operations meetings
- Andon Boards with relevant information
Result
- Real-time visualization of the entire production
- Immediate response options
- Quick and easy access to information
- Employee involvement
Faster adaptation and more comprehensive overview
It was extremely difficult for the company to quickly adapt to new requirements. The low transparency and flexibility in manufacturing led to problems often being identified too late. This made it challenging for employees to react in a timely and efficient manner. Without a comprehensive overview of the status and production-relevant information, it was nearly impossible to manage production processes smoothly and efficiently.
Maximum transparency and flexibility
“The whole system is designed to maximize transparency and flexibility,” says Martin Zennig, Head of Automation IT and Software Development and the platform’s technical manager. Depending on the settings, the software can show a high-level view of the entire production plant, individual production lines or individual machines, including all relevant production data such as statuses, production orders currently in progress, units produced and quality. Visual Shop Floor selectively forwards information in real time to whoever is responsible. The data can be accessed simply and at any time on a PC, tablet or smartboard.
Visual Shop Floor also has its own meeting module, which is used for daily operations meetings around the smartboard in the production hall. Based on the visualizations shown on the smartboard, engineering and manufacturing staff work with the production management to analyze outcomes and reports and define what needs to be done each day. Information of importance to the employees is displayed on large screens in the production facility.
With Visual Shop Floor the whole production plant at a glance
The digital visualization of the entire production, displaying the status and all production-relevant information in detail in real time – that is Visual Shop Floor. This software solution has been in place at the TPS Business Group's sensor facility in Berlin since 2017. The advantage is that employees have a clear overview of all production operations at all times – and can respond immediately if any deviations occur.
Being able to access digital information quickly and easily at any time delivers all kinds of benefits for the workforce: “Visual Shop Floor is an excellent tool to quickly and clearly display complex production data,” explains Jan Lamla, Director Transmitter Operations Engineering.
Ongoing expansion
Visual Shop Floor has been continually improved and developed since it was first implemented. “The size of our production facility in Beeskowdamm alone has tripled to about 3,500 square meters in this period,” says Sven Siedenburg, Head of Transmitter Operations and NTCs in Berlin. That meant constantly incorporating new machines in the system. But it also meant continually adding extra functionality.
In the next step, Visual Shop Floor will also display cleanroom parameters such as temperatures and carbon dioxide concentrations. Additionally, plans exist to introduce the system at the sensor facility in Batam in Indonesia and at TDK Electronics subsidiary Tronics Microsystems in Crolles in France. Corresponding knowledge has likewise been transferred to the CAP Business Group, whose capacitor plant in Gravataí in Brazil is already integrated in Visual Shop Floor.
Our employees see their feedback flowing straight into the system. They are actively shaping the digital transformation, which generates two positive effects at the facility. transitioning step by step to Industry 4.0 and involving our employees in the process.”
Sven Siedenburg,
Head of Operations Transmitter and NTCs in Berlin, TDK Electronics
Flexibility and scalability as the key to success
4 reasons why TDK Electronics benefits from the flexibility and scalability of Visual Shop Floor.
Visual Shop Floor has been continuously expanded and developed since its introduction
Important and newly identified use cases are being consistently implemented
New locations are gradually integrated into Visual Shop Floor
TDK Electronics is constantly working on implementing small improvements at regular intervals