At NetQM, a high-tech full-service provider in the field of mechatronics with locations in Austria and Bosnia and Herzegovina, Solunio's software Visual Shop Floor has become an important tool in quality management.
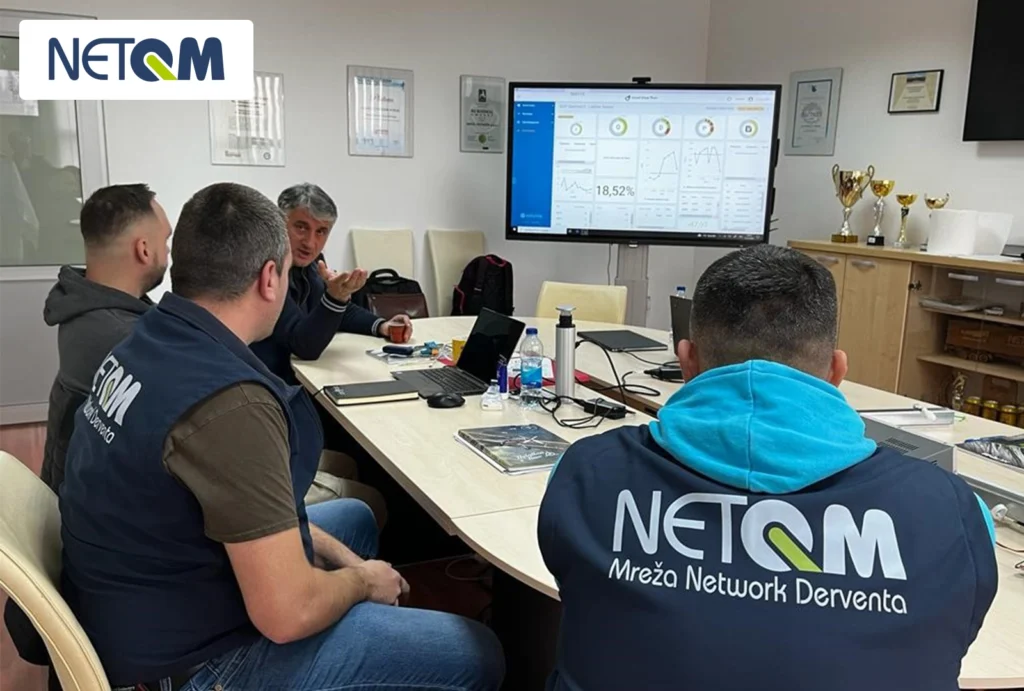
NetQM, Visual Shop Floor in action – Dashboard
NetQM is a high-tech full-service provider in the field of mechatronics. The group of companies with locations in Austria and Bosnia and Herzegovina develops and produces technologically complex series parts from product development to prototype construction to series production. The portfolio covers the areas of cable assembly, electronics, mechanics and injection moulding as well as individual special developments. Customers come from the automotive industry, racing, telecommunications, medical technology and many more. The company employs 400 people. The headquarters are located in Puch near Hallein, the production site in Bosnia and Herzegovina.
NetQM, production site, Bosnia & Herzegovina
Challenge
- Many stand-alone workstations
- Lots of paper instead of digital information
- Outdated and incomplete information
- No data visualization capabilities
Solution
- Visualization and consolidation of scattered data
- Easy interfaces to various systems
- Live data display in daily meetings
- Andon boards with real-time quality metrics
Result
- Real-time monitoring of production data
- Immediate identification of root causes
- Deviation analysis of target times
- Cross-border data exchange and communication
- Unified standards
From isolated data silos to a centralized solution
Many stand-alone workplaces that were not really connected. A lot of paper instead of digitized information. And thus hardly any possibilities to visualize and meaningfully evaluate the data. The company NetQM wanted to change these general conditions and take the internal processes a step further towards digitalization: “Our goal was to centralize and, above all, visualize the information that was floating around distributed in the different departments. Instead of the individual data islands, we wanted to create a digital platform where the data is brought together,” explains project manager Lukas Höller-Strasser from the company NetQM.
“In the past, the shift and department managers met at shift changes with pen and paper to check and update the data. To be honest, I have to say that the update was not always implemented.” As a result, NetQM often worked with outdated and incomplete information.
Visual Shop Floor – the data octopus
During the search for suitable software to address this challenge, NetQM came across the company Solunio and its Visual Shop Floor software platform. “In the end, this solution convinced us because it brings together and visualizes the scattered data via simple interfaces from the systems like a data octopus,” says Lukas Höller-Strasser. The various data from the ERP system are consolidated by Visual Shop Floor and processed into useful information for quality management.
Screens in production – the focal point
Today, Visual Shop Floor displays the collected data live on screens during daily meetings, revolutionizing communication and decision-making processes. Around 80 strategically placed screens visualize current quality metrics in the form of Andon Boards. "We are currently using the software intensively in quality management to precisely define where and how improvements should be implemented. Visual Shop Floor became the central player in this process and is now our basis for optimization steps," says Lukas Höller-Strasser.
In the end, this solution convinced us because it brings together and visualizes the scattered data via simple interfaces from the systems like a data octopus.
Lukas Höller-Strasser,
Project Manager, Network Quality Management (NetQM)